Royal DSM: CAPEX
Meeting sustainability standards and financial hurdles at the new Caprolactam (CPL) facility in China
In 2013, following a €200m investment, DNCC (Royal DSM’s joint venture with Sinopec) opened a new 200 kilo ton per annum capacity facility in Nanjing for producing Caprolactam (CPL), a chemical used in the manufacture of nylon. The investment came about in response to market growth opportunities in the region. By going beyond minimum local regulatory requirements, we constructed a production line that is upheld as a model of sustainable engineering across Royal DSM’s global business, whilst maintaining attractive financial returns.
Sustainability sets the bar
Being sustainable was not a ‘nice-to-have.’ The CPL facility was subject to strict permit requirements regarding wastewater effluent, air pollution, greenhouse gas emissions and energy efficiency. Failure to meet these would put our licence to operate at risk. Environmental factors were qualifiers, not differentiators. To meet these regulatory requirements, as well as our own internal standards, the project team designed the facility with sustainability features including a wastewater treatment and effluent recovery plant, phosphate removal unit, N2O removal installation and heat recovery technologies.
Commercial drivers
Whilst sustainability was essential, commercial value remained a primary driver. The project was subject to standard financial hurdles for major capital investments. Our research and development team were brought on board to seek opportunities that satisfied both commercial and sustainability goals. We identified technological improvements that would increase production yields whilst minimising resource use, emissions and waste.
The compatibility of sustainability and commerciality
Our plant shows that enhancing sustainability can be consistent with minimising cost and, therefore, compatible with commercially-driven investments. Moreover, making sustainability a core driver of project design, resulted in a facility that not only has good financial returns, but is also by far the most environmentally friendly CPL production line in Royal DSM’s asset portfolio. Compared to a standard design, the new facility uses 37% less fresh water and 20% less energy, and generates 58% less effluent waste.
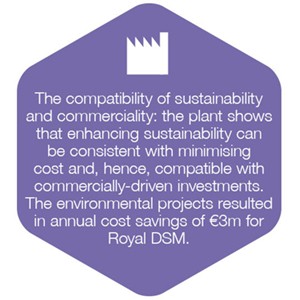