Danone: Strategic Planning, Budgeting and Forecasting
ESTABLISH SYSTEM AND FUNCTIONALITY REQUIREMENTS FOR EFFICIENT ACCESS TO REQUIRED DATA
Danone’s Executive Board sees sustainability as a strategic priority. We have adopted a measured approach to integrating sustainable business practices across our 160 plants on five continents in over 120 countries. We’ve established carbon reduction as a guiding principle, and have appointed a ‘Vice President for Nature’. Senior management has elevated carbon reduction to coequal status with business targets, and also works hard to optimize water usage, which is key to operations. Transparency to consumers and retailers, as well as support for new standards and legislation in the countries where we operates, are foundational to our strategy of growth driven by sustainability.
To help achieve this transformation, we have partnered with SAP to help make sustainability an integral part of how we do business every day. The two companies are united by a shared commitment to innovative IT strategies that will meet our promises to consumers and the challenges of today’s environment, as well as comply with changing country regulations. In a resource constrained world where consumers want to make better choices, both companies know sustainability is not only about conservation or recycling. Real change can only occur by taking a measured business approach to determine the cost of materials and products across the supply chain, from sourcing to production to delivery and beyond.
As a result, Danone implemented SAP ERP to collect, measure, analyse and reduce our carbon footprint across our entire 35,000 product line. Relying on several SAP modules, the process captures highly detailed, monthly assessments of our product line by stock keeping unit (SKU) across the entire lifecycle, from sourcing through production, transport, retail distribution, consumption and end of lifecycle. Full integration with SAP ERP allows us to automatically retrieve information including bills of materials, production and delivery orders and intercompany transportation. We can easily assess a range of product footprints, and incorporate allocation of emissions and costs generated by each process.
We also use SAP ERP to help holistically manage data collection, reporting and analytics across all social, environmental and economic initiatives. Danone is also working with suppliers so they can directly enter their data into SAP ERP, saving time and boosting information quality. Future plans include enhanced reporting beyond SKU carbon footprint tracking. We will report emissions by product, factory, division, country, brand, customer and time interval, then set benchmarks based on the intelligence. Executives envision a monthly ‘sustainability closing’, much like a financial closing, for greater transparency and stronger competitive advantage.
Implementing SAP software solutions has helped to drive employee engagement. Employees have a deeper sense of pride in their work since every staff member is held accountable for the quality of carbon data in their business area. Specialists in lifecycle management collect and assess information from the supply chain, such as site specific emission factors for components used during the raw pack process. People with job titles like Carbon Master and Master Data Manager, along with users in manufacturing, purchasing and transport units, provide additional input for things like emissions factors by transport types or energy consumption to complete the process. Teams perform calculations for insight and visibility into the carbon measurements at a product level via multidimensional modelling and analysis. Using SAP software reports and dashboards, employees can display the product carbon footprint intensity as grams of CO2e per kilogram or litre of product, as well as in absolute terms of metric tonnes of CO2e emissions.
As a result, Danone implemented SAP ERP to collect, measure, analyse and reduce our carbon footprint across our entire 35,000 product line. Relying on several SAP modules, the process captures highly detailed, monthly assessments of our product line by stock keeping unit (SKU) across the entire lifecycle, from sourcing through production, transport, retail distribution, consumption and end of lifecycle. Full integration with SAP ERP allows us to automatically retrieve information including bills of materials, production and delivery orders and intercompany transportation. We can easily assess a range of product footprints, and incorporate allocation of emissions and costs generated by each process.
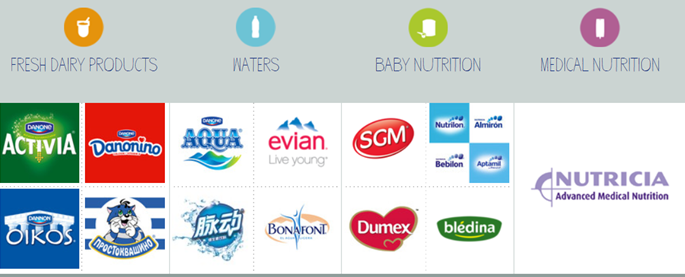
As a result, Danone implemented SAP ERP to collect, measure, analyse and reduce our carbon footprint across our entire 35,000 product line. Relying on several SAP modules, the process captures highly detailed, monthly assessments of our product line by stock keeping unit (SKU) across the entire lifecycle, from sourcing through production, transport, retail distribution, consumption and end of lifecycle. Full integration with SAP ERP allows us to automatically retrieve information including bills of materials, production and delivery orders and intercompany transportation. We can easily assess a range of product footprints, and incorporate allocation of emissions and costs generated by each process.
We also use SAP ERP to help holistically manage data collection, reporting and analytics across all social, environmental and economic initiatives. Danone is also working with suppliers so they can directly enter their data into SAP ERP, saving time and boosting information quality. Future plans include enhanced reporting beyond SKU carbon footprint tracking. We will report emissions by product, factory, division, country, brand, customer and time interval, then set benchmarks based on the intelligence. Executives envision a monthly ‘sustainability closing’, much like a financial closing, for greater transparency and stronger competitive advantage.
Implementing SAP software solutions has helped to drive employee engagement. Employees have a deeper sense of pride in their work since every staff member is held accountable for the quality of carbon data in their business area. Specialists in lifecycle management collect and assess information from the supply chain, such as site specific emission factors for components used during the raw pack process. People with job titles like Carbon Master and Master Data Manager, along with users in manufacturing, purchasing and transport units, provide additional input for things like emissions factors by transport types or energy consumption to complete the process. Teams perform calculations for insight and visibility into the carbon measurements at a product level via multidimensional modelling and analysis. Using SAP software reports and dashboards, employees can display the product carbon footprint intensity as grams of CO2e per kilogram or litre of product, as well as in absolute terms of metric tonnes of CO2e emissions.